New Ethernet Protocol Keeps the Industrial IoT in Sync
- Srinivasa Rao Nookala
- Dec 24, 2018
- 3 min read
Factory machines will use time-sensitive networking to coordinate their work
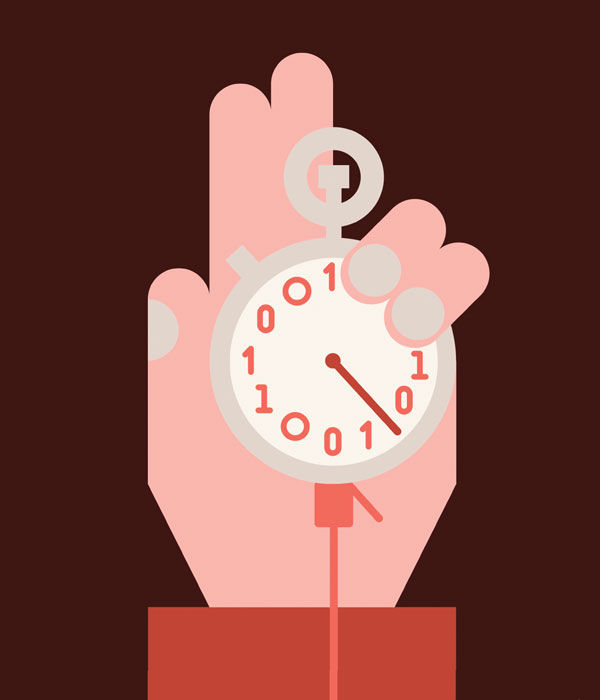
Timing is the unsung hero of the Internet. Timing enables syncing databases halfway around the world, trading stocks from thousands of miles away and allowing calls and data to traverse mobile networks undistorted. Understanding when a packet of information is sent and how to reassemble packets in the correct order when they’re received is crucial to our modern networks.
And now timing has to take the best of the Internet and marry it with the rigors and reliability of the factory-automation network as manufacturers bring in more information technology to their existing factory-automation systems. One way to do that is through an emerging standard called time-sensitive networking, which embeds a shared understanding of time into devices connected by Ethernet.
Traditionally, for highly accurate timing, you place quartz timing chips in every piece of equipment or force each machine to call back to the cloud to get the time. But quartz-based clocks on every machine in a factory would be too expensive, and calling back to a cloud-based clock is not secure. That’s why engineers are turning to Ethernet and time-sensitive networking.
If Ethernet can help machines deliver the right message in a specified amount of time, it can eliminate dozens of pricey proprietary protocols used today. Different industrial machines often have their own data protocols, and being able to replace them with one Ethernet-based protocol can also bring better scale and distribution benefits to the world of industrial-technology protocols.
The proprietary protocols in traditional factory automation emphasize reliability and speed. After all, if a machine has a problem it needs to quickly shut off or send an alert to avoid an expensive mistake or a potential workplace safety issue. Real time really matters.
However, for the IT networks that companies are now trying to bring into factories, the emphasis is typically on cost-effective technologies such as Ethernet that do their best to deliver information without any specific guarantee of quality. Unlike the protocols for factory automation, these networks are designed to gather all of the information at a switch before passing it along the network. So the network might slow down for a bit while a software update is delivered, and in the case of a highly congested network, the data may not get delivered at all.
But factories can’t afford buffering or missed packets between their machines, which is why the IEEE is adding time-sensitive networking protocols to the Ethernet standard. Time-sensitive networking helps prioritize different types of traffic so machine traffic can take precedence over a nonessential software update or a file sync.
I first saw demonstrations of the technology in early 2017 at National Instruments’ Industrial IoT Lab, but it has since gained ground in many manufacturing areas. In October 2018, Texas Instruments released anembedded processor for factory equipment that enables time-sensitive networking at gigabit speeds. A month later the OPC Foundation, which is trying to create a unified protocol for factory automation, said it would standardize the movement of data in its OPC UA protocol over time-sensitive networks.
Pekka Varis, chief technologist for catalog processors at Texas Instruments, says that factories might soon have one Ethernet cable replacing the two networks that currently handle IT and operational technology.
Two years ago, I would have said this would never happen, but the market for time-sensitive networks is growing. I suppose you should never bet against Ethernet.
This article appears in the January 2019 print issue as “Keeping the Industrial IoT in Sync.”
Comments